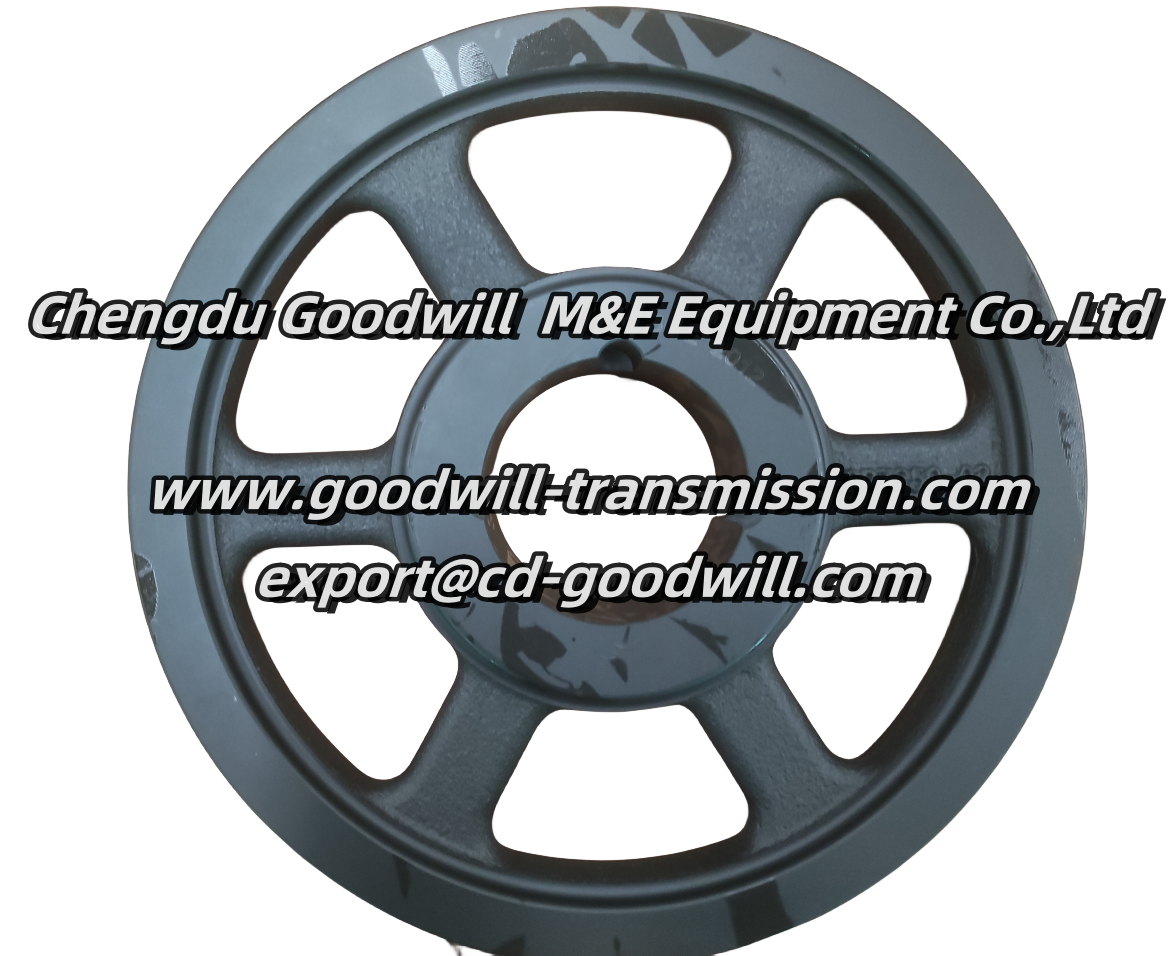
V-belt pulleys (also called sheaves) are fundamental components in mechanical power transmission systems. These precision-engineered components efficiently transfer rotational motion and power between shafts using trapezoidal V-belts. This professional reference guide provides comprehensive technical information about V-belt pulley designs, standards, specifications, and proper selection criteria.
1. V-Belt Pulley Construction and Anatomy
Core Components
Grooved Rim
Features precisely machined V-shaped grooves matching belt profiles
Groove angles vary by standard (38° for classical, 40° for narrow section)
Surface finish critical for optimal belt grip and wear characteristics
Hub Assembly
Central mounting section connecting to the drive shaft
May incorporate keyways, set screws, or specialized locking mechanisms
Bore tolerances maintained to ISO or ANSI standards
Structure
Solid Hub Pulleys:Single-piece design with continuous material between hub and rim
Spoked Pulleys:Features radial arms connecting hub to rim
Web Design Pulleys:Thin, solid disc between hub and rim
Material Specifications
Cast Iron (GG25/GGG40)
Most common industrial material offering excellent vibration damping
Steel (C45/St52)
For high-torque applications requiring superior strength
Aluminum (AlSi10Mg)
Lightweight alternative for high-speed applications
Polyamide (PA6-GF30)
Used in food-grade and noise-sensitive environments
2. Global Standards and Classifications
American Standard (RMA/MPTA)
Classical V-Belt Pulleys
Designated by letters A (1/2"), B (21/32"), C (7/8"), D (1-1/4"), E (1-1/2")
Standard groove angles: 38° ± 0.5°
Typical applications: Industrial drives, agricultural equipment
Narrow Section Pulleys
3V (3/8"), 5V (5/8"), 8V (1") profiles
Higher power density than classical belts
Common in HVAC systems and high-performance drives
European Standard (DIN/ISO)
SPZ, SPA, SPB, SPC Pulleys
Metric counterparts to American classical series
SPZ ≈ A section, SPA ≈ AX section, SPB ≈ B section, SPC ≈ C section
Groove angles: 34° for SPZ, 36° for SPA/SPB/SPC
Narrow Profile Pulleys
XPZ, XPA, XPB, XPC designations
Correspond to 3V, 5V, 8V profiles with metric dimensions
Widely used in European industrial equipment
3. Technical Specifications and Engineering Data
Critical Dimensions
Parameter | Definition | Measurement |
Pitch Diameter | Effective working diameter | Measured at belt pitch line |
Outside Diameter | Overall pulley diameter | Critical for housing clearance |
Bore Diameter | Shaft mounting size | H7 tolerance typical |
Groove Depth | Belt seating position | Varies by belt section |
Hub Protrusion | Axial positioning reference | Ensures proper alignment |
Performance Characteristics
Speed Limitations
Maximum RPM calculated based on material and diameter
Cast iron: ≤ 6,500 RPM (dependent on size)
Steel: ≤ 8,000 RPM
Aluminum: ≤ 10,000 RPM
Torque Capacity
Determined by groove count and belt section
Classical belts: 0.5-50 HP per groove
Narrow belts: 1-100 HP per groove
4. Mounting Systems and Installation
Bore Configurations
Plain Bore
Requires keyway and set screws
Most economical solution
Common in fixed-speed applications
Taper-Lock® Bushings
Industry-standard quick-mount system
Accommodates various shaft sizes
Eliminates need for keyways
QD Bushings
Quick-detachable design
Popular in maintenance-heavy environments
Requires matching shaft diameter
Installation Best Practices
Alignment Procedures
Laser alignment recommended for critical drives
Angular misalignment ≤ 0.5°
Parallel offset ≤ 0.1mm per 100mm span
Tensioning Methods
Proper tension critical for performance
Force-deflection measurement
Sonic tension meters for precision
5. Application Engineering Guidelines
Selection Methodology
Determine Power Requirements
Calculate design HP including service factors
Account for start-up torque peaks
Identify Space Constraints
Center distance limitations
Housing envelope restrictions
Environmental Considerations
Temperature ranges
Chemical exposure
Particulate contamination
Industry-Specific Applications
HVAC Systems
SPB pulleys with dynamic balancing
Food Processing
Stainless steel or polyamide construction
Mining Equipment
Heavy-duty SPC pulleys with taper-lock bushings
6. Maintenance and Troubleshooting
Common Failure Modes
Groove Wear Patterns
Uneven wear indicates misalignment
Polished grooves suggest slippage
Bearing Failures
Often caused by improper belt tension
Check for excessive radial loads
Preventive Maintenance
Regular visual inspections
Vibration analysis for critical drives
Belt tension monitoring systems
For further technical assistance or to request our engineering design guide, please contact our technical support team. Our engineers are available to help specify the ideal pulley solution for your specific application requirements.
Post time: Apr-03-2025