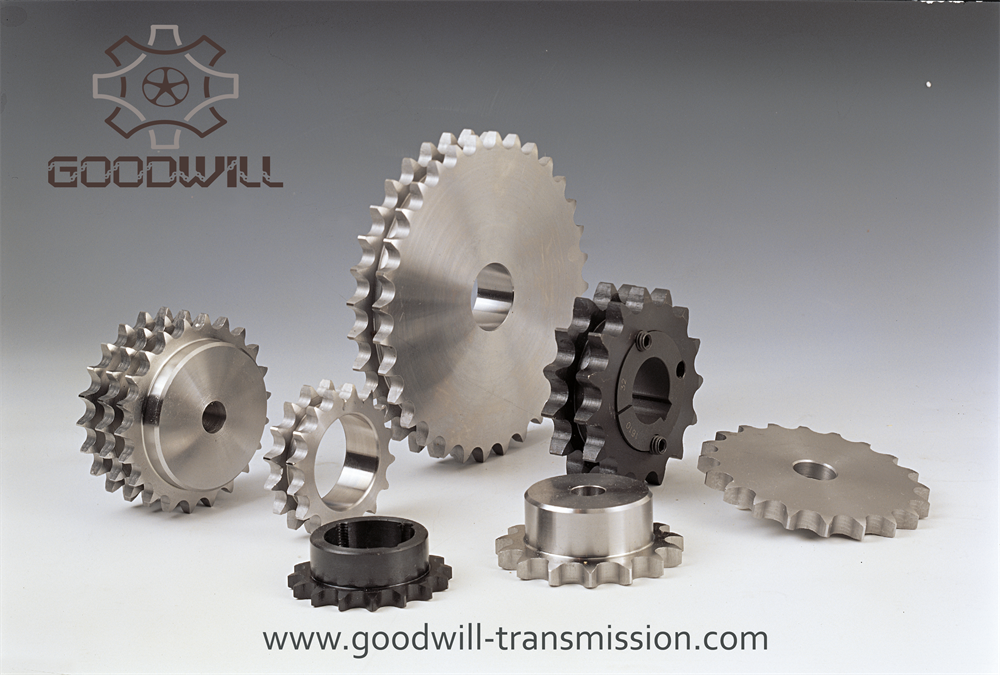
When it comes to maximizing the efficiency and longevity of your mechanical systems, the choice of chain sprockets is paramount. Let’s dive into the essential aspects of materials, dimensions, structures, and maintenance that will elevate your operations to new heights.
Material Selection: When it comes to optimizing your mechanical systems, the choice of chain sprocket materials is crucial. You want to ensure that the teeth of your sprockets possess sufficient contact fatigue strength and wear resistance. That’s why high-quality carbon steel, such as 45 steel, is often the go-to choice. For those critical applications, consider upgrading to alloy steels like 40Cr or 35SiMn for enhanced performance.
Most sprocket teeth undergo heat treatment to achieve a surface hardness of 40 to 60 HRC, ensuring they can withstand the rigors of operation. It’s important to note that smaller sprockets engage more frequently than their larger counterparts and face greater impacts. Therefore, the materials used for small sprockets should be superior to those used for larger ones.
For sprockets that need to endure shock loads, low-carbon steel is an excellent option. On the other hand, cast steel is ideal for sprockets that experience wear but don’t face severe impact vibrations. If your application demands high strength and wear resistance, alloy steel is the way to go.
Investing in the right materials for your chain sprockets not only enhances their longevity but also boosts the overall efficiency of your mechanical systems. Don’t compromise on quality—choose wisely and watch your performance soar!
Key Dimensions and Structural Choices
Understanding the primary dimensions of your sprockets is essential for optimal performance. Key dimensions include the number of teeth, pitch circle diameter, outer diameter, root diameter, tooth height above the pitch polygon, and tooth width. The pitch circle is the circle on which the center of the chain pins lies, evenly divided by the chain pitch. As shown below:

Sprockets come in various structural forms, including solid, perforated, welded, and assembled types. Depending on the size, you can choose the appropriate structure: small diameter sprockets can be solid, medium diameter sprockets often use a perforated design, and large diameter sprockets typically combine different materials for the tooth ring and core, connected through welding or bolting. For specific examples, check out Goodwill’s sprocket catalogues.
Tooth Design: The Heart of Efficiency
The number of teeth on a sprocket significantly impacts transmission smoothness and overall lifespan. It’s crucial to select an appropriate number of teeth—not too many and not too few. An excessive number of teeth can shorten the chain’s lifespan, while too few can lead to unevenness and increased dynamic loads. To mitigate these issues, it’s advisable to limit the minimum number of teeth on small sprockets, typically set at Zmin ≥ 9. The number of teeth on small sprockets (Z1) can be selected based on chain speed, and then the number of teeth on the large sprocket (Z2) can be determined using the transmission ratio (Z2 = iZ). For even wear, sprocket teeth should generally be an odd number.

Optimal Chain Drive Layout
The layout of your chain drive is just as important as the components themselves. The common layout of chain drive is shown below

Horizontal Layout: Ensure that the rotation planes of both sprockets are aligned within the same vertical plane and that their axes are parallel to prevent chain disengagement and abnormal wear.
Inclined Layout: Keep the angle between the centerlines of the two sprockets and the horizontal line as small as possible, ideally less than 45°, to avoid poor engagement of the lower sprocket.
Vertical Layout: Avoid having the centerlines of the two sprockets at a 90° angle; instead, offset the upper and lower sprockets slightly to one side.
Chain Positioning: Position the tight side of the chain on top and the slack side below to prevent excessive droop, which could lead to interference with the sprocket teeth.
Tensioning for Optimal Performance
Proper tensioning of the chain drive is vital to prevent excessive droop, which can lead to poor engagement and vibrations. When the angle between the axes of the two sprockets exceeds 60°, a tensioning device is typically employed.
There are various methods for tensioning, with the most common being adjusting the center distance and using tensioning devices. If the center distance is adjustable, you can modify it to achieve the desired tension. If not, a tensioning wheel can be added to adjust the tension. This wheel should be placed near the slack side of the small sprocket, and its diameter should be similar to that of the small sprocket.
The Importance of Lubrication
Lubrication is essential for the optimal performance of chain drives, particularly in high-speed and heavy-load applications. Proper lubrication significantly reduces wear, mitigates impacts, enhances load capacity, and extends the lifespan of the chain. Therefore, it is crucial to select the appropriate lubrication method and type of lubricant to ensure efficient operation.
Lubrication Methods:
Regular Manual Lubrication: This method involves using an oil can or brush to apply oil to the gaps between the inner and outer link plates on the slack side of the chain. It is recommended to perform this task once per shift. This method is suitable for non-critical drives with chain speeds of v ≤ 4 m/s.
Drip Oil Feed Lubrication: This system features a simple outer casing, where oil is dripped into the gaps between the inner and outer link plates on the slack side through an oil cup and pipe. For single-row chains, the oil supply rate is typically 5-20 drops per minute, with the maximum value used at higher speeds. This method is appropriate for drives with chain speeds of v ≤ 10 m/s.
Oil Bath Lubrication: In this method, a non-leaking outer casing allows the chain to pass through a sealed oil reservoir. Care must be taken to avoid submerging the chain too deeply, as excessive immersion can lead to significant oil loss due to agitation and may cause the oil to overheat and deteriorate. An immersion depth of 6-12 mm is generally recommended, making this method suitable for drives with chain speeds of v = 6-12 m/s.
Splash Oil Feed Lubrication: This technique utilizes a sealed container where oil is splashed up by a splash plate. The oil is then directed to the chain via an oil collection device on the casing. The immersion depth of the splash plate should be maintained at 12-15 mm, and the splash plate speed should exceed 3 m/s to ensure effective lubrication.
Pressure Lubrication: In this advanced method, oil is sprayed onto the chain using an oil pump, with the nozzle strategically positioned at the point where the chain engages. The circulating oil not only lubricates but also provides a cooling effect. The oil supply for each nozzle can be determined based on the chain pitch and speed by consulting relevant manuals, making this method suitable for high-power drives with chain speeds of v ≥ 8 m/s.
To achieve optimal performance and efficiency in your mechanical systems, it is essential to understand the critical aspects of chain sprocket selection and maintenance. Don’t leave the success of your machinery to chance—make informed decisions that yield lasting results!
Selecting the right materials, dimensions, and maintenance strategies is key to ensuring your operations run smoothly and efficiently. By prioritizing these factors, you can enhance the longevity and reliability of your equipment.
If you have any questions about sprockets or need expert guidance, please don’t hesitate to reach out to us at export@cd-goodwill.com. Our dedicated team is here to assist you with all your sprocket needs!
Post time: Nov-21-2024